Five-axis CNC machine tools in automotive parts processing efficiency enhancement
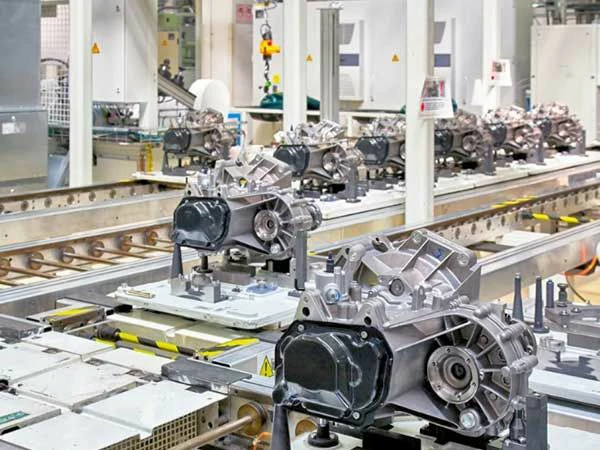
Enhancing Efficiency in Automotive Parts Processing with Five-axis CNC Machine Tools
Introduction
As the automotive industry continues to evolve and demand for high-quality parts increases, manufacturers are constantly seeking ways to enhance their production efficiency. One technology that has revolutionized the field is the use of five-axis CNC (Computer Numerical Control) machine tools. These advanced machines offer a range of benefits that enable automotive part manufacturers to optimize productivity, improve precision, and reduce costs. In this article, we will explore how the utilization of five-axis CNC machine tools has contributed to efficiency enhancement in the automotive parts processing industry.
Improved Flexibility and Versatility
The first key advantage of five-axis CNC machine tools is their enhanced flexibility and versatility. Traditional machining methods often require multiple setups and tool changes to complete complex parts, leading to inefficiencies and increased production time. However, with five-axis CNC machines, manufacturers can achieve complex machining tasks in a single setup. The ability to rotate and tilt the workpiece allows for intricate and precise machining operations from multiple angles, eliminating the need for manual intervention or adjustments.
Enhanced Precision and Accuracy
Precision and accuracy are vital in the automotive industry, where components must fit together seamlessly to ensure optimal performance and safety. Five-axis CNC machines excel in delivering exceptional precision due to their advanced control systems and simultaneous multi-axis motion capabilities. By utilizing five axes of movement, these machines can approach the workpiece from various angles, reducing the chances of errors and maintaining consistent dimensions. This level of precision is particularly crucial when manufacturing critical parts such as engine components, transmission systems, and suspension systems.
Reduced Production Time and Costs
Another significant advantage of using five-axis CNC machine tools is the substantial reduction in production time and costs. With traditional machining methods, the need for multiple setups and tool changes can significantly slow down the production process. In contrast, five-axis CNC machines can complete complex operations in a single setup, eliminating time-consuming manual intervention. This results in shorter lead times and increased manufacturing throughput. Additionally, the improved precision and accuracy offered by five-axis CNC machines reduce material waste and rework, leading to cost savings in the long run.
Streamlined Workflow and Increased Productivity
The integration of five-axis CNC machine tools into the automotive parts processing workflow has also contributed to improved productivity. These machines can perform a wide range of machining operations, including milling, drilling, turning, and contouring, all in a single setup. The ability to complete multiple operations in one go reduces idle time and maximizes machine utilization. Moreover, the advanced control systems and software automation allow for efficient toolpath generation, optimizing cutting strategies and minimizing cycle times. As a result, manufacturers can achieve higher productivity levels without compromising quality or accuracy.
Conclusion
The utilization of five-axis CNC machine tools has revolutionized the automotive parts processing industry, enhancing efficiency, precision, and productivity. With their improved flexibility, enhanced precision, reduced production time, and streamlined workflow, these machines have become invaluable assets for manufacturers. As the automotive industry continues to evolve, the adoption of five-axis CNC machine tools will undoubtedly play a crucial role in meeting the increasing demands for high-quality components while maintaining cost-effectiveness.
.webp)